RT
Every Successful Roofing Projects has TWO requirements
ONE- Quality Roofing Materials
TWO- A Quality Contractor
ROOFING MATERIAL TYPES
Built Up Roofing (BUR): Traditionally, flat roofs have been installed by setting 3-4 layers of asphalt-saturated felt (“tar-paper”) in a mopping of hot asphalt. When topped with a final layer of “90lb Cap Sheet” it is often referred to as a “Cap Sheet BUR Roof”. Originally, the top surfacing is gravel set in a flood-coat of hot asphalt.
Single-Ply Membranes: Over the past 30 years, a wide variety of roofing membranes have been developed, using various forms of synthetic rubber (EPDM), reinforced plastic and vinyl plastic. The seams are typically formed on site, using adhesives, tapes, or hot-air welding. Some are available in different colors, and can be manufactured in wider rolls in an effort to minimized the number of seams.
TPO is a widely used roof of this roofing variety. These TPO roofs are often reasonable in cost and white in color. However, you will need to have installed a tapered insulation system in order to eliminate standing water if it is present. This is because standing water will most often void a manufacturers warranty on this roofing type. Since they are new to the industry, some say they have a spotty track record. You will need to study up on the specific TPO system(s) being offered by contractors. They are NOT all the same.
Modified Bitumen: These membranes are still asphalt-based materials, but plasticizers have been added to improve strength, flexibility, water-resistance, etc. They can be incorporated into a conventional BUR, or applied as a single-ply membrane. Often these are adhered to the roof with the use of a Torch. Unfortunately, this process has occasionally resulted in a fire hazard.
Spray in Place, Polyurethane Foam roofing systems. These systems add insulation to a building and typically are white in final color. They are self flashing and can be applied so as to substantially reduce standing water. Unlike the other roofing systems, these are renewable by simply applying additional roof coating at the end of their warranty periods. Once re-coated the contractor and manufacturer will extend their warranties. With a 40+ year history, these are quickly becoming the roof of choice.
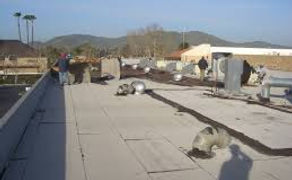
This is a 90# Cap Sheet type Roof.

This is an EPDM type Roof.

This is a TPO type Roof.

This is a Torch Down Mod Bit type Roof.
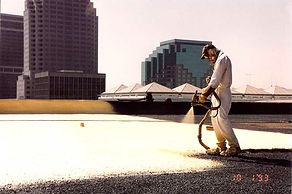
This is a Spray in Place Foam type Roof.
Silicone Coating: An application of Silicone Coating over all of the above roofing systems once they have started to fail and started leaking will produce good long term results. This roofing repair is both long lasting and often is backed by the Silicone manufactures 10,15 or even 20 year labor and material no leak warranty! Additionally, it doesn't require the removal and re-installation of roof mounted A/C or existing Solar panels. Also, in many jurisdictions it isn't considered as a 3rd roof due to its light weight properties so a roof tear off isn't required. With its final heat reflective "Cool Roof Compliant" white color, it is a good choice in regions where summer time air conditioning demands are high driving up utility costs.

This is a Silicone Coated Roof with a GE 15 year Labor and Material warranty.
QUALITY CONTRACTORS & WARRANTIES
Quality Contracting Companies with a history of success, will most always be designated as “Qualified Applicators” by those manufacturers of materials they are installing. They should be ready to provide an extensive history of successful projects with the materials they propose to install on your roof.
Once the have completed their roof installation they will generally provide a labor and materials NO LEAK warranty. They may range in length from 10 to 20+ years. These can often be very good, especially if the building owner is named “additionally insured” on the contractors liability insurance and it is of an “Occurrence Form”. Look for a warranty that is NOT a prorated type, meaning it reduces in value as time goes by. Ask your insurance agent about the importance of “Occurrence” vs. “Claims made” forms of liability insurance coverage and the protection it affords you.
The property owner is sometimes issued a “Manufacturers” warranty as well. These can be very useful, especially if the material manufacturer sends out a representative to inspect the completed roofing installation and approves its quality.
Since many “flat roofs” hold water, it is important that the “manufacturers” warranty doesn’t exclude problems caused by that standing water. If that is the situation, make sure that the roofing contractor has eliminated “inadequate or insufficient drainage” as part of their roofing process by correcting the roofs drainage problems in order to avoid these exclusions. As always, the details are in the fine print.